Learning by Design Doing at TU Delft
Share
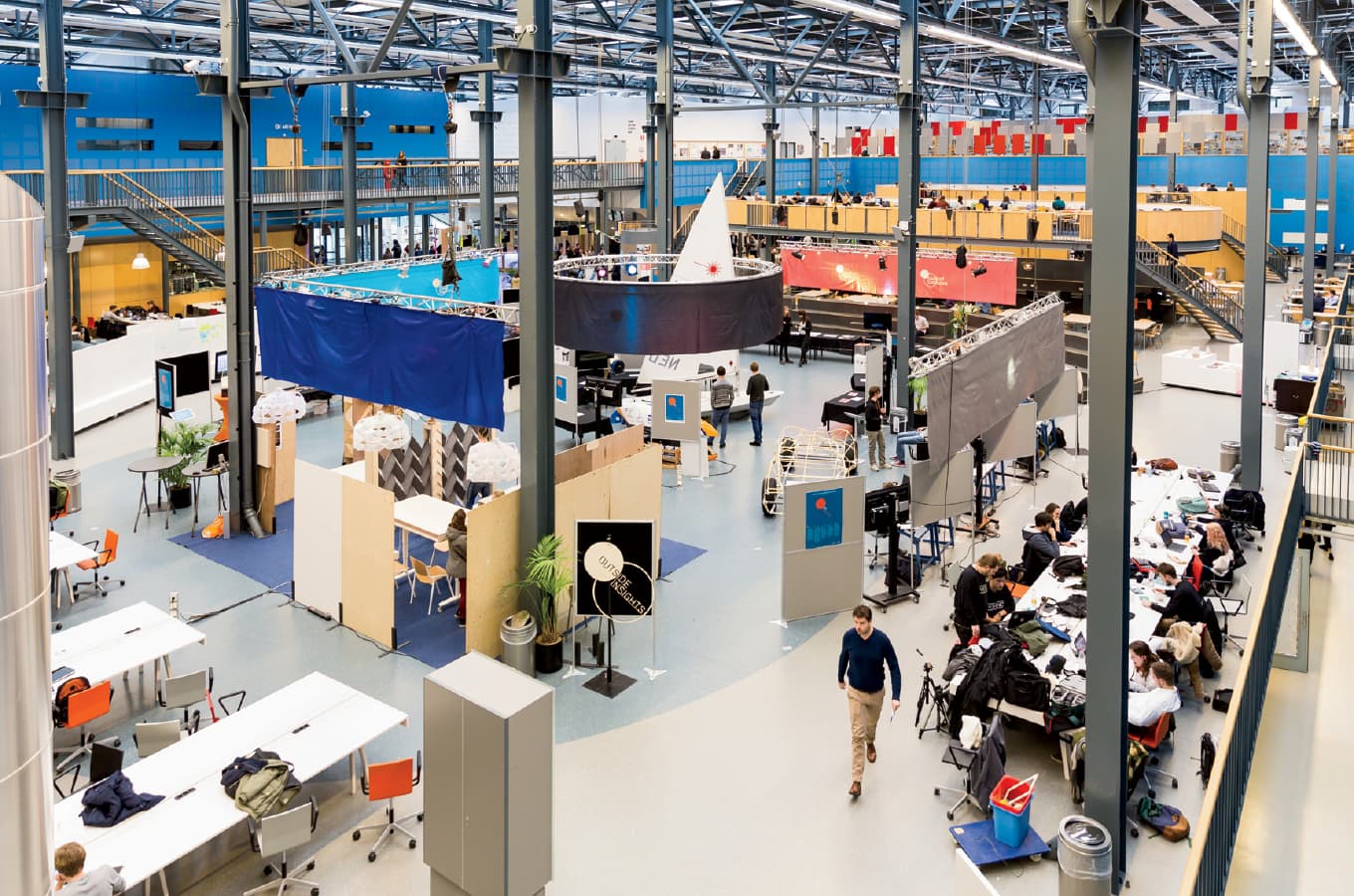
TU Delft’s collaborations with the likes of KLM and Zodiac Aerospace are providing its Industrial Design Engineering students with hands-on experience while offering the industry a window into the next generation of ideas.
TU Delft may be the oldest Dutch public technological university, but its Industrial Design Engineering department has never been too bothered by tradition when it isn’t useful. The faculty headquarters is designed like an arena, with a wraparound balcony on the second story that encircles and overlooks the main area that connects to a number of classrooms, workshops, offices and labs, including a Consumer Research Product Evaluation lab, Model-Making and Machine lab and a Physical and Ergonomics lab.
When the building opened in the 1970s, the central area was used as a workshop for large pieces of machinery, giving the work of engineers pride of place. The heavy equipment may no longer be there, but the machinations of designers at work are still front and center via regular exhibitions and collaborative work sessions in the space. The ground floor library isn’t filled with books, instead, a variety of materials supplied by around 200 companies can be touched and toyed with.
“We’ve got a really hands-on approach,” says Katinka Bergema, a postdoc researcher in the Department of Product Innovation Management where she specializes in networked innovation, collaboration, aviation and baggage. To help students get their hands dirty, the faculty facilitates collaborations with relevant companies such as Airbus, Boeing, Zodiac Aerospace, KLM, BMW and even Adidas. “We collaborate intensively with the industry to make our work relevant and provide students with a real-life contact to work in,” she says.
“The naivety of the students, in the positive sense, helps to not only see the limitations of all kinds of solutions, but to see the opportunities it creates,” Bergema explains. “Students don’t care whether they need organization A or B, or department A or B, or about all the politics involved. They just want to have a solution and involve who they need to. This helps to actually realize their ideas.”
Extracurricular Curriculum
Approximately 120 students work on aviation projects each year in different courses and degrees. In the elective course Service Design Process run by Christine De Lille, Froukje Visser and Julia Debacker, students are challenged to design new services from the perspectives of stakeholders while prioritizing the needs of passengers and crew. Through guest lectures and excursions to partner company sites, students develop an appreciation for industry tools and standards, and learn at an early stage how to pitch their ideas to large organizations. The course, which takes 35 students at a time, can be so popular that students are asked to provide a statement on why they’re interested in signing up.
One project developed in the course, “Sense the Transitions,” a multisensory, interactive in-flight entertainment (IFE) experience, nabbed a Crystal Cabin Award in 2014. Developed for long-haul flights, the concept draws upon research that revealed up to 50 percent of screen time in flight is devoted to watching the flight map.
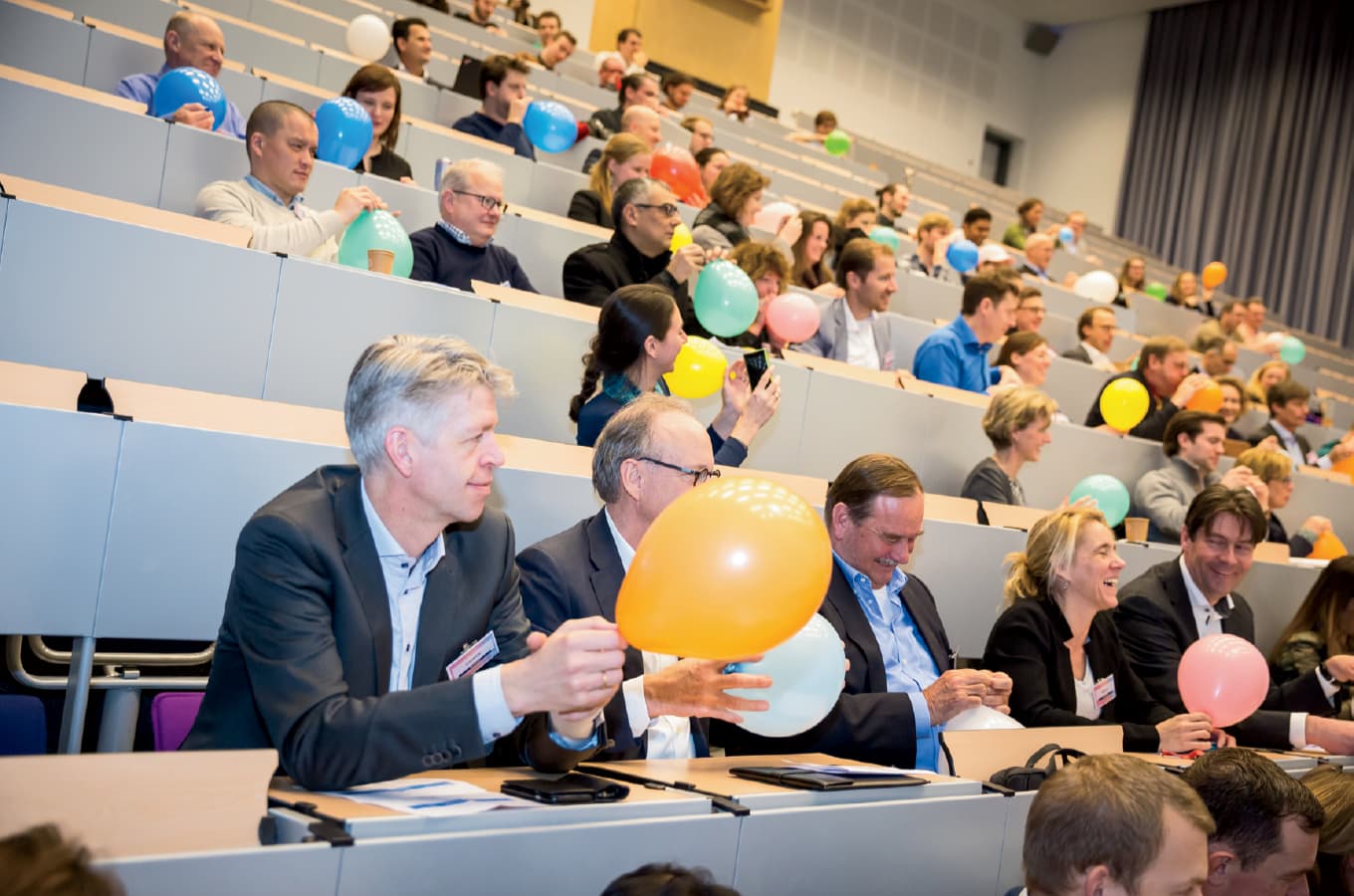
In partnership with Zodiac Aerospace, Anna-Louisa Peters, Karan Shah and Dorine van Meeuwen developed a location-responsive geotainment system that displays footage of the places passengers fly over. Different thematic channels such as culture, nature, cuisine or history and pop-ups with useful tips and factoids allow viewers to delve into topics that interest them.
For his master’s thesis, Xander van der Broek decided to investigate the hand luggage surplus problem KLM brought to TU Delft. With carry-on baggage becoming more popular, the airline found that one in every seven of its flights could not accommodate the amount of bags passengers were bringing. Through studies conducted with the airline and Luggage lab, van der Broek analyzed the potential luggage capacity of each aircraft type in KLM’s fleet and was able to pinpoint why the problem occurred on specific flights.
In his research he observed that the practice of gate-checking excess baggage not only aggravated passengers, but gate agents tended to overcompensate and check more bags than necessary, so he used his capacity data to develop a gate-check calculator tool to help agents be more accurate. His study also found that passengers were willing to check their hand luggage if it didn’t incur any fees, a finding that he used to recommend methods for decreasing the inflow of carry-on bags.
The X Factor
The “real world” experiences students have access to in these courses is undoubtedly a powerful recruiting tool for TU Delft where overall enrollment has steadily been on the rise. For students, the competitive advantage of earning a diploma and enhancing their curriculum vitae simultaneously has led a majority of graduates to find employment within three months. Some students even graduate with a patent filing to their name: In 2015, 80 inventions and 39 patent applications were submitted, 22 contracts were signed on the basis of patents and33 patents were commercialized.
The hardheaded and somewhat unconventional pragmatism of TU Delft’s Industrial Design Engineering faculty is impacting the way its corporate partners research and innovate as well. “The industry is realizing the potential of design,” explains Christine De Lille, assistant professor at the university. “Aviation organizations are focusing more and more on passenger experience, on technology as a means, and on the future. Design is a key way to integrate all these aspects and translate this into hands-on solutions.”
De Lille cites a thesis project by Basil Vereecke, conducted in partnership with Zodiac Aerospace, as an example. With the goal of helping Zodiac shift to user-centered design practices, Vereecke helped develop the Zodiac Experience Lab, with an expanded product development and R&D department, in Alkmaar, Netherlands, where it is now frequently in use. There is now a second location in Toulouse, France.
The department’s strongest and probably most reciprocal corporate partnership has been with KLM. The decades-long history between the two organizations was recently formalized with the announcement that the department would enter a five-year collaboration agreement. “About 20 months ago, we stopped having meetings at KLM,” says Sander Stomph, KLM’s director of Operational Excellence. “Instead we created different spaces where employees, clients, TU Delft students and the KLM X team could experience the best solution to change something, or find the best way to launch a project.”
Last year, around 175 TU Delft students worked on-site with KLM on tackling different problems, including prototyping new versions of the My Flights section of its website at boarding gates, or developing an improved communications system for flight crew. In turn, KLM employees – including many TU Delft alumni – are visiting the university to learn and connect on their shared philosophy of “design doing.” In working together on these projects, the teams translated KLM’s agile design sprints into a five-step solution process called KLM X. The process, says Stomph, involves not just theorizing about design and having numerous meetings, “but actually doing things that make the KLM and passenger experience better.”
“Working with TU Delft has helped us get to the core of a problem much more quickly.” – Marissa Gubler, KLM
“Working with TU Delft has helped us get to the core of a problem much more quickly and move faster to the ideation phase, which in turn means that we can actually implement the solution faster,” says Marissa Gubler, a product owner in the Digitizing Passenger Operations division at KLM. Gubler and her team worked with master’s students on a digital solution called PLUG aimed at improving gate crew communications and leading to time savings of 90 percent. Now in use, Gubler expects communications to be 80 percent more effective.
The benefits for the students, university and company in these collaborative partnerships are clear, but Bergema and De Lille insist that at the end of the day, design is about the end user. “We put the passenger and the future central to the work we do,” says Bergema. “Since we’re not a party with commercial interest, we can easily bring all stakeholders together and take developments to the next step.”
“Learning by Design Doing” was originally published in the 7.3 June/July issue of APEX Experience magazine.